SOP3 with Co-Packing Project Manager Johnny Montana
In this episode of the Econo-Pak Contract Food Packaging Podcast, Sarah Richter sits down with Project Manager Johnny Montana and GM Mike Mead to discuss the importance of SOP3 (Standard Operating Procedure Form 3) in ensuring food safety, quality, and seamless production.
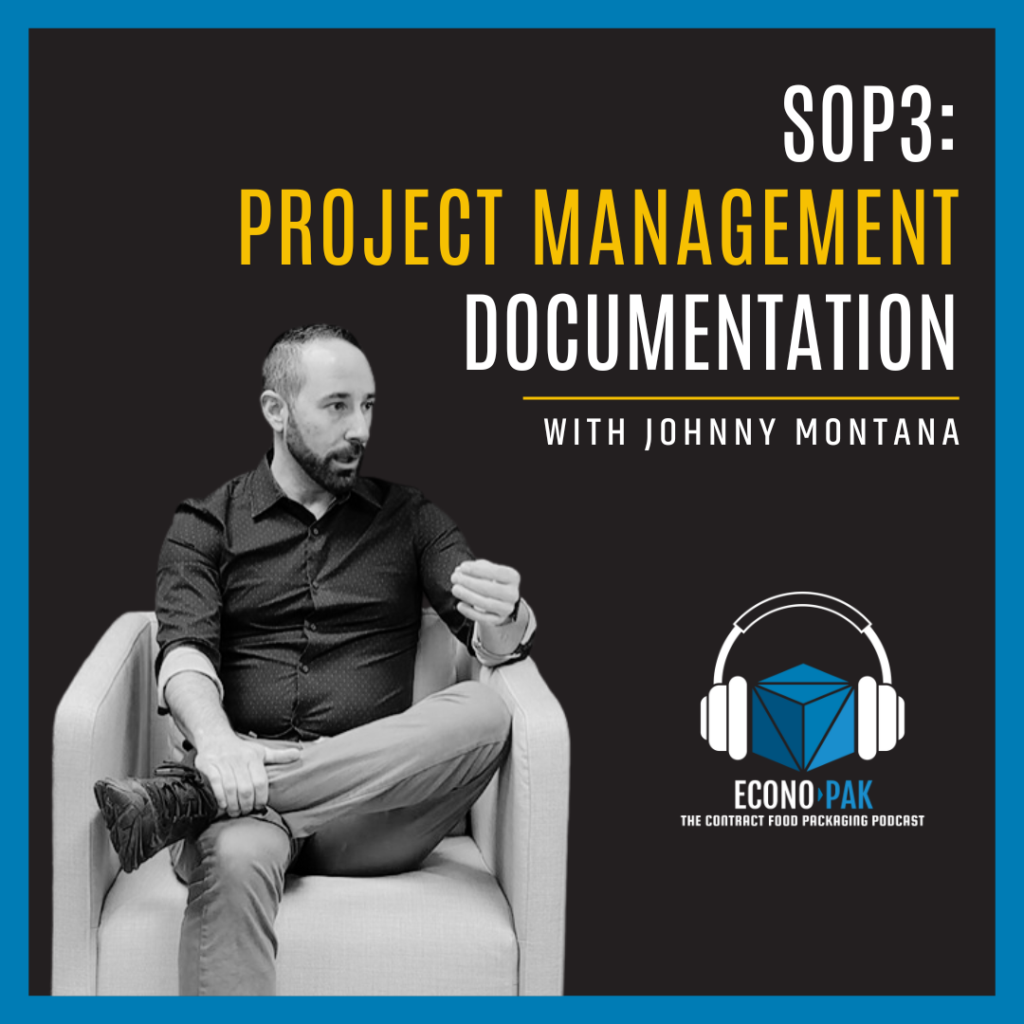
Understanding SOP3: Ensuring Quality and Food Safety in Co-Packing
Sarah Richter: Welcome to the Econo-Pak Contract Food Packaging podcast. Today we’re here with Johnny Montana, our project manager, and we’re going to be talking about SOP3 today. How are you?
Johnny Montana: Alright. Thank you for having me. Happy to go over some of these details with you.
What is SOP3?
Sarah Richter: Yeah. So maybe you could explain what the SOP3 is, what it stands for, and how it’s used?
Johnny Montana: Absolutely. SOP3 stands for Standard Operating Procedure form 3. It’s a form we use with new customers and existing customers who have new projects. It captures all the details for a project we’re about to produce for a customer.
How does SOP3 tie into quality and processes?
Sarah Richter: Awesome. And how does that tie into quality and the processes around it?
Johnny Montana: Great question. SOP3 is heavily quality-related. Quality collaborates with all the departments to develop this form. It captures quality data, customer service data, and production data. This ensures we have all the necessary information to produce a project without missing any details. As an official form, it also captures food safety information critical to processing correctly.
How is SOP3 used across departments?
Mike Mead: Great. And that also goes into other departments as well, obviously quality being the key factor, as Sarah mentioned, but it’s also used by other departments.
Johnny Montana: Correct.
Mike Mead: Customer service?
Johnny Montana: Yes. Customer service uses it when setting up a new customer or a new project in the system. The SOP3 includes information like SKU numbers for finished goods and inbound details so we can receive components into our system. All of this information is documented there.
How does the team collaborate on SOP3?
Sarah Richter: Yeah. So does quality help craft the SOP3?
Johnny Montana: Absolutely. Once we receive a completed SOP3, we sit down as a team—myself, quality, and customer service for that specific customer. We review it together to ensure there are no missing details, corrections needed, or questions.
We make sure to review it collectively as a team rather than just shuffling it between departments. This way, everyone is on the same page.
Why is it important for clients to complete SOP3 accurately?
Sarah Richter: From a client’s perspective, why is it important for them to fill it out with attention to detail?
Johnny Montana: Great question. In the contract food packaging world, food safety is crucial, and nobody knows the details of their product like the customer does. They can provide critical information for their product that we might not have.
However, we don’t just hand them the form and expect them to fill it out alone. We act as partners, always willing to sit down and go through the SOP3 with them to clarify any questions.
How does SOP3 address unique client needs?
Mike Mead: Yeah, I was going to ask about the most important questions on there, but honestly, it seems like all of them are crafted to be important.
Johnny Montana: Correct. Some sections might not apply to every customer, which is why sitting down with them can be helpful. SOP3 is a comprehensive form designed for multiple food packaging types, so while not every question is relevant to all projects, those that are applicable are essential.
Sarah Richter: That’s a great point. I was going to ask about the unique needs of our diverse clients—from different packaging configurations to various dry food products. Whether it’s a new product or something established, it’s important to address all those differences.
Johnny Montana: Absolutely. With the variety of packaging styles we offer—horizontal and vertical bagging, blending, mixing, seasoning—SOP3 captures all the necessary details for each specific project.
When is SOP3 completed in the co-packing process?
Sarah Richter: During the project process, when do we complete the SOP3?
Johnny Montana: SOP3 is completed before production begins. After a customer reaches out with a new project, we go through pricing and feasibility phases. If the project is a good fit, we complete the SOP3 before any trials, fitment tests, or production startup. This ensures accuracy and alignment with the customer’s needs.
SOP3: A critical piece of every project
Mike Mead: And we have an SOP for everything, correct?
Johnny Montana: Correct. Every project we handle has an SOP3.
Mike Mead: That’s fantastic. From small to large projects, having this documentation available and digitized is crucial.
Sarah Richter: Especially as an SQF level 3 co-packer.
Mike Mead: Absolutely. It’s a critical piece.
Sarah Richter: Awesome. Well, thank you so much for joining us today, Johnny. We really appreciate it.
Johnny Montana: No problem. Happy to be here. Thank you.
Let's start scaling.
Is your demand outpacing your ability to package your own product? Then consider outsourcing with Econo-Pak.
With over 40 years of experience working with both small brands and Fortune 500 companies, we are capable of handling your specific dry food product.
Get in touch with our team for a fixed-price quote for your project.